How To Prevent And Avoid Burnout In Your Manufacturing Plant
Try When I Work for free
2021 was a pressure-filled year, with manufacturing bearing the brunt of it on many fronts.
In the midst of closures and constantly changing safety requirements during the pandemic, manufacturing plants had to stay open. They produced the world’s essential goods despite the challenges of regulations, quarantined employees, supply chain problems, and shipping delays.
Some of that is still going on, but there’s something new added to the mix. There’s a labor shortage.
“Now Hiring” signs are posted everywhere. In fact, there are roughly 500,000 manufacturing positions open. That means increased pressure on everyone as manufacturing employees feel the pressure to meet production timelines, but without enough staff to help them.
It’s no wonder, in light of all of this, that burnout and stress are on the rise. And that ends up being expensive for manufacturing businesses both in financial and human capital.
There are several studies that back this up. Stress and anxiety, along with depression, are the reason for most work-related illnesses and employee sick days. Another study connected employee burnout to the main reason businesses failed to build a fully engaged workforce. 95% of surveyed HR experts agreed that burnout and stress end up destroying workplace retention.
We’re talking serious absenteeism, frustrated and disengaged employees with lower productivity, and a revolving door leaving you constantly in a state of hiring and replacing workers. In other words, stress and burnout hurt your employees and ruin your chances to build an engaged and reliable workforce.
Those are hard statistics.
Addressing burnout isn’t optional, but neither is it an easy problem to solve during a labor shortage when demands are higher than usual. Fortunately, there are a few basic things you can do to address stress and burnout in a way that can make your manufacturing plant not only stable, but actually thrive and be competitive when it comes to attracting new hires.
Share the resources your employees need
Sometimes employees don’t recognize burnout for what it is.
It comes off as frustration, apathy, or some other form of stress. Even if they know it’s burnout, they might not feel like they can tell anyone, and that they have to just figure it out on their own. Burnout that isn’t addressed will lead to quitting.
Helping employees who are burnt out isn’t difficult.
Start by talking to your employees about burnout. Help them know what it looks like, and that it’s for real. Keep an eye out for signs employees are struggling. Maybe you’ll do it by sharing articles and information, including useful tools like meditation apps or links to TED talks. Perhaps you’ll share booklets or information in the breakroom. Definitely provide links to your employee assistance program (EAP) and encourage them to make use of those resources.
Whatever you do, don’t create a punitive system—intentionally or not—that punishes employees who are trying to deal with burnout. The goal is to let your employees know you care about them, and to help them be more self-aware of what they’re experiencing.
Failure to address employee burnout is harmful to your business, but that’s not your only motivation. It’s not just because you want fewer sick days or better retention, but because you care about your employees’ actual well-being.
Review your workplace culture
Workplace culture makes or breaks any business.
Take two identical businesses and, by changing the workplace culture, you can turn one into an employee magnet while the other is completely toxic. It’s all about how management and employees get along, and whether everyone is on the same page.
You need to review the culture at your plant, and find areas you could improve.
- Do you manage your employees with empathy and respect? Do you show it tangibly?
- How do you see them? As individuals with unique needs?
- Is there more focus on production and deadlines instead of on human factors?
- Do your employees know what you expect of them, or are they operating on unclear assumptions?
- Are employees given a path to voicing concerns or ideas without fear?
- Do employees think you care about their work-life balance?
The biggest signs of cultural failure is if your employees don’t know what you expect them to do, and if your decisions are production first, people second.
There are other benefits when you improve and maintain a great work culture, particularly when it comes to how it impacts your bottom line. But first and foremost, it’s about making the workplace somewhere your employees want to be, a place they feel safe and able to do their best without reprisal.
Consider your employees when creating production timelines
A labor shortage mixed with high demand is the perfect storm when it comes to creating inhumane production timelines.
Yes, you have production levels you have to meet. There’s no getting around it. But you can work with your production management team to align your timelines with your staff hours and availability.
That means, if you’re understaffed, you take that into account. You don’t over promise to buyers. You don’t forge ahead with your production as if you have a full staff, assuming things are temporary and that your employees won’t burn out before you get back to “normal.”
Setting impossible timelines and production goals will drive your employees away. Remember, there’s a labor shortage. If production is grinding them down, they can easily find jobs elsewhere.
Use staffing companies to fill in the gaps
Managers might enjoy bragging about how many hours their employees work, but they really shouldn’t. Forcing excessive hours on your team is nothing to be proud of.
There will be times that, no matter how hard you’ve worked on your culture, on employee retention, and on adjusting production requirements, you simply have staffing gaps that are going to put pressure on your employees.
That’s where temporary staffing can help.
Look for a staffing agency to partner with you regularly to fill your entry-level production positions. That way you can use your regular employees to focus on work that requires more expertise, and the temp employees you bring in become used to the work you need from them.
If you’re not convinced that temp employees are necessary, consider the safety issue.
In July 2021, Frito Lay workers went on strike because they were being asked to pull 84-hour work weeks to meet consumer demand, despite being short staffed. Even being offered time-and-a-half or triple time wasn’t enough to solve the issue, because demanding extremely long shifts, particularly over an extended period of time, is completely unsustainable. If you don’t fill the staffing gaps, you run the risk of not only burnout, but also dangerous working conditions from exhausted employees or product recalls.
It is much better to use temporary staffing to meet demand instead.
Use flexible scheduling
One of the best ways to improve workplace culture and ward off weariness, is to use flexible scheduling.
Consider what your employees have observed during the pandemic. White-collar workers have been able to work from home, enjoying the benefits of a better work-life balance that come with that kind of schedule.
Meanwhile, your employees, as essential workers, didn’t get that chance. Worse, current high demand and labor shortages are skewing it further against a shot at better work-life balance.
While you can’t create a work from home option for your plant workers, you can introduce flexibility into your work schedule and give them more control over when they work.
Flexible self scheduling gives employees more control over their own schedules. That means they have some say in what they do with their personal lives instead of having a work schedule that always overrides it. They can pick the shifts they want, and swap with other coworkers. That helps stave off feelings of burnout, builds a sense of team, and keeps them more engaged. Manufacturing scheduling software can make it easier for you to offer flexible self scheduling.
Imagine if you’re a potential employee. Would you choose the place that dictated the schedule with no feedback, or the place that offered flexibility in their schedule as a benefit? It’s a simple way for you to stand out from the crowd vying for the attention of potential workers.
Download our manufacturing flexible scheduling guide to learn how it works.
Simplify your manufacturing schedule and keep employees happy.
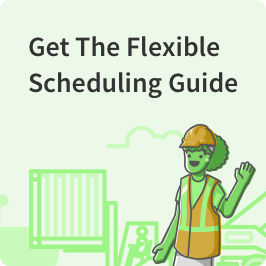
Employee burnout feels inevitable right now. The good thing is that, by putting a system in place to address it, you are setting yourself up to stand out in a packed field of competition in the midst of a labor shortage.
Flexible scheduling is an easy way to accomplish this, and When I Work can help you get up and running very quickly.